Il modo migliore per trivellare un pozzo per l'acqua dipende dalla vostra tipo di terreno specifico, profondità dell'acqua prevista, budget e condizioni geologiche.. Non esiste un unico metodo che funzioni al meglio ovunque. Per pozzi poco profondi, sotto i 100 metri, in terreni soffici, Impianti di perforazione portatili offre una semplicità a basso costo. Per pozzi più profondi o terreni instabili, perforazione a rotazione con viscosità del fango ottimizzata fornisce velocità e stabilità del foro, soprattutto oltre i 140 metri. Tecniche avanzate come pompa a circolazione inversa eccellere nelle aree sabbiose/silvatiche riducendo al minimo i rischi di crollo. La combinazione di un'adeguata analisi del sito, di una tecnologia appropriata alla profondità e di misure preventive contro i crolli offre i risultati più sicuri ed efficienti.
Fase 1: analisi del terreno e della geologia
Condizioni ideali sono terreni profondi e privi di rocce con una falda freatica medio-alta. I terreni sciolti, come sabbia o ghiaia, consentono un'elevata resa idrica, ma devono essere abbastanza densi da filtrare l'acqua piovana. Evitare i luoghi con:
- Sedimenti non consolidati: La sabbia, la ghiaia o il limo sciolti si infiltrano facilmente nel foro di trivellazione.
- Argilla pesante o sabbia fine: Richiedono un controllo preciso del fango per evitare il restringimento del foro.
- Roccia fratturata o grandi massi: Il fango di perforazione può scorrere nelle fessure, destabilizzando le pareti.
Rilievo della topografia del terreno Le pendenze o gli affioramenti rocciosi nelle vicinanze fanno presagire sfide nel sottosuolo. In Ghana, ad esempio, gli strati di granito o di arenaria quarzosa richiedono punte di perforazione specializzate e casing a gradini.
Fase 2: scegliere i metodi di perforazione in base alla profondità
Gamma di profondità | Il miglior metodo di perforazione | Perché funziona |
---|---|---|
< 100 metri | Impianti di perforazione portatili | Attrezzatura semplice e a basso costo; solleva i residui di taglio meccanicamente con una punta pesante |
< 140 metri | Pompa a circolazione inversa | Veloce, economico; l'aspirazione rimuove efficacemente i detriti nei terreni più morbidi |
> 140 metri | Impianti di perforazione idraulica | La rotazione ad alta potenza taglia la roccia dura; stabilizzata dal fango di perforazione |
Pozzi profondi (>200 metri) può essere necessario motori downhole per la precisione, anche se possono sorgere problemi di tenuta.
Fase 3: prevenire il crollo del foro
Crollo del pozzo è una delle principali cause di fallimento. Combattetela con:
- Ottimizzazione del fango di perforazione: La miscela bentonite-acqua deve essere sufficientemente viscosa da sostenere le pareti, ma abbastanza sottile da poter circolare. Troppo spessa? Si frattura la roccia. Troppo sottile? Le pareti cedono. Monitorare costantemente: aggiungere acqua per assottigliare o bentonite per addensare.
- Utilizzo di un involucro temporaneo: Schermatura di sezioni instabili in terreni sciolti fino alla posa del rivestimento permanente.
- Evitare le vibrazioni nelle zone deboli: Passare a strumenti a basso impatto se si formano crepe.
Suggerimento: se una buca crolla, recuperare rapidamente gli strumenti utilizzando overshots + vasi di profondità. In caso di incastro, eseguire un nuovo foro di trivellazione: il recupero è spesso più costoso.
Fase 4: seguire una sequenza di perforazione comprovata
Foro pilota: Eseguire un foro guida stretto, quindi alesare fino alla dimensione completa, soprattutto nella roccia dura.
Installare l'involucro e lo schermo: Impedisce l'afflusso di sedimenti. In acquiferi sabbiosi, aggiungere pacchetti di ghiaia all'esterno del filtro.
Sviluppare il pozzo: Pompa/sovralimentazione aggressiva per rimuovere i residui fini e massimizzare la resa.
Qual è il metodo più efficiente?
- Velocità: Foratura rotativa > Circolazione inversa > Utensile a cavo.
- Costo: La circolazione inversa è vincente per i pozzi <140 m; la rotazione diretta è migliore oltre questo limite.
- Stabilità: I fluidi HPWBF riducono il rischio di collasso di 60% in scisti e rocce fratturate.
Conclusione: Il "modo migliore" è su misura
Abbina il tuo geologia del sito e obiettivo di profondità al metodo:
- Sabbia/sabbia <100m? Utilizzare l'utensile a cavo o la circolazione inversa.
- Roccia dura >150m? Optare per la perforazione a rotazione con HPWBF.
- A rischio di collasso? Dare priorità al controllo del fango e al rivestimento temporaneo.
Test in locale-Effettuare una trivellazione di prova con campionamento di carote se la geologia è incerta. Collaborate con trivellatori esperti nelle peculiarità della vostra regione, come il granito del Ghana o gli scisti dell'Ohio.
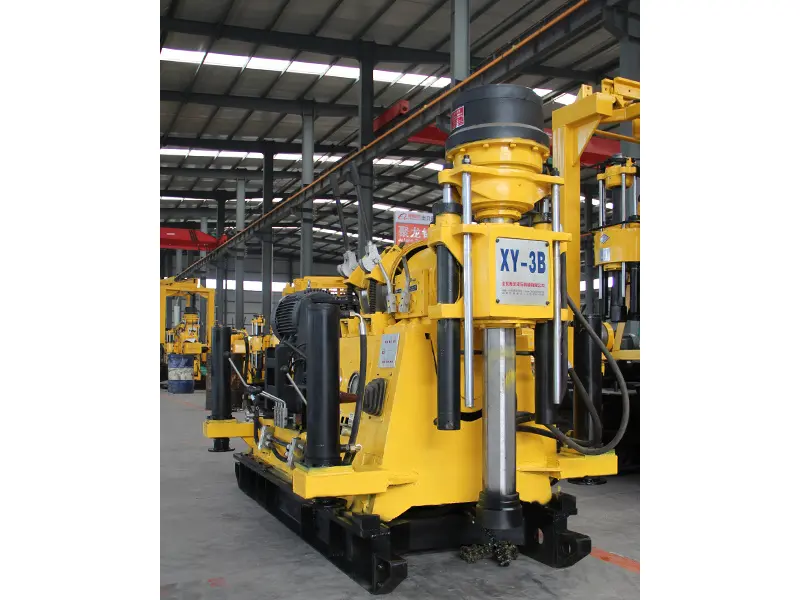