Air drilling—using compressed air instead of liquid mud to remove cuttings—boasts faster penetration rates and lower costs in hard formations. But its disadvantages of air drilling include serious operational risks that can offset these benefits. Ignoring these drawbacks leads to costly well control incidents, equipment failures, and project delays. This article uncovers the critical limitations you must plan for, using field data and engineering analysis.
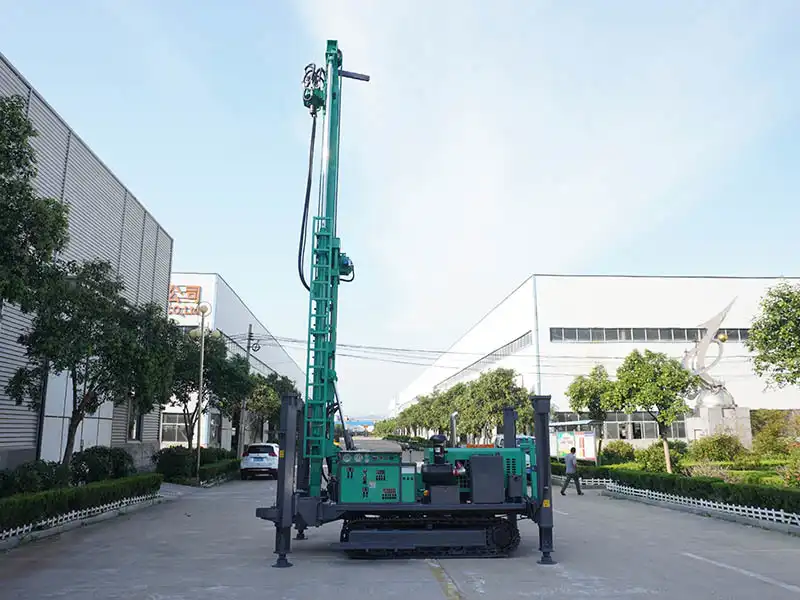
Unstable Wellbores Formation Collapse and Instability Risks
Air lacks the density and viscosity to mechanically support fragile formations. Unlike drilling fluids, it doesn’t create a hydrostatic pressure barrier or a filter cake to seal micro-fractures. In shale, clay, or poorly consolidated sands, this leads to:
Caving and sloughing: Water-sensitive shales absorb atmospheric humidity from the air stream, swelling and collapsing into the borehole. In Inner Mongolia operations, formations with >15% clay content showed 40% higher instability rates compared to mud-drilled sections.
Hole enlargement: Unsupported walls erode from high-velocity air streams (>15 m/s), creating oversized holes that complicate cementing and increase casing costs.
Stuck pipe incidents: In China’s Xiaoqinling gold fields, borehole instability caused 30% of air-drilling-related stuck pipe events. Remediation averaged 72 hours of non-productive time (NPT).
Accelerated Equipment Erosion: The High Price of High Velocity
Air’s low carrying capacity demands high annular velocities (1,500–3,000 ft/min) to lift cuttings. This turns the wellbore into a sandblasting chamber:
BHA erosion: Drill collars, stabilizers, and tool joints suffer micro-cutting wear. Hard-banding materials erode 2–5x faster than in mud drilling. Field metallurgy tests in Sichuan Basin showed 0.12 mm/hour metal loss in directional assemblies.
Surface line damage: Blowout preventer (BOP) seals, choke manifolds, and compressors degrade from abrasive dust. Operators in Colorado’s Piceance Basin reported 60% shorter BOP service life under air drilling.
Erosion “hot spots”: Changes in flow direction (subs, elbows, tees) intensify wear. Downhole camera inspections in Appalachian gas wells revealed 3 mm deep grooves in drill pipe after 150 hours.
Downhole Fires and Explosions Ignition Triggers
Compressing air heats it to >500°F—enough to ignite flammable mixtures. Adding only 5% hydrocarbons creates explosive conditions:
Bit fires: Pyrophoric iron sulfides (from sulfur-bearing formations) spark upon contact with oxygen. A 2022 West Texas incident ignited a bottomhole assembly fire, melting drill string tools.
Coal seam risks: Methane releases in coalbed methane (CBM) projects caused 12 documented well fires in Australia’s Bowen Basin during air-drilled segments.
Mitigation costs: Nitrogen generation units—reducing oxygen to <5%—add $15,000–$25,000/day. Foam systems lower explosiveness but increase water consumption by 300 bbl/day.
Formation Damage Water Blocking and Permeability Loss
Though touted as “reservoir friendly,” air introduces formation damage mechanisms:
Water blocking: Downhole humidity condenses in pore throats. In low-permeability gas reservoirs (0.1–5 mD), this cut production by 30% in Utah’s Uinta Basin wells versus mud-drilled offsets.
Clay swelling: Air-delivered moisture activates smectite clays. Post-drill core analysis in Colombia’s Llanos Basin showed 90% permeability reduction in swelling-prone zones.
Hydrocarbon oxidation: Oxygen reacts with light oils, forming viscous tar that clogs pores. Canadian operators noted 25% lower initial production rates in air-drilled horizontal laterals.
Dust and Cuttings Management: Environmental Headaches
Air drilling produces 10–20 tons/hour of fine rock dust, creating visible plumes and safety hazards:
Silica exposure: Dust with >5% crystalline silica exceeds OSHA Permissible Exposure Limits (PELs) within 500 ft of the rig. Sampling at Pennsylvania shale sites showed 0.8 mg/m³—double the PEL.
Waste volumes: While “no fluid pits” is a selling point, foam-assisted air drilling generates 400–800 bbl/day of fluid waste—similar to low-volume mud systems.
Noise pollution: Compressors and exhausts produce 110–125 dBA. Communities in Germany’s Molasse Basin halted projects over noise complaints.
Stuck Pipe and Downhole Complications
Low lubricity and high friction make air drilling prone to mechanical sticking:
Differential sticking: Despite no overbalance, cuttings beds pack around the BHA. At China’s Zijinshan Mine, 22% of air RC drilling NPT derived from cuttings-induced sticking.
Keyseat embedment: Hard formations develop sharp wellbore ledges that trap drill strings. Remediation requires specialized tools like rotary shoes or milling—adding $50,000–$120,000 per incident.
Limited logging: Air’s low density distorts neutron porosity tools by 8–15 pu. Resistivity tools fail without conductive mud.
When Air Drilling Costs More: The Economic Paradox
Air drilling isn’t universally cheaper. Hidden expenses erode savings:
Cost Factor | Air Drilling | Mud Drilling |
---|---|---|
Daily Rig Rate | $25,000 | $20,000 |
Compression/N2 Costs | $18,000/day | $0 |
Drill Pipe Replacement | 40% faster wear | Baseline |
Well Control (per incident) | $500,000 (fire/lost hole) | $150,000 (kick) |
Waste Disposal | $2–$8/bbl (foam systems) | $4–$10/bbl |
Source: SPE 208905 (2023 cost analysis of Permian Basin wells)
In deep wells (>12,000 ft), air’s ROP advantage diminishes as pressure control complexities escalate.
Mitigation Strategies Reducing the Disadvantages
Managed Pressure Drilling (MPD) hybrids: Maintain near-balanced pressure with air-mist, reducing influxes while keeping ROP 2–3x higher than mud.
Erosion-resistant tooling: Tungsten carbide hard-facing extends BHA life by 200%. Regular UT inspections catch thickness loss early.
Downhole dehumidification: Air-drying units suppress formation hydration. Trials in Oman’s tight gas fields lowered water-blocking by 70%.
Dust suppression systems: Wet scrubbers or misting rings cut silica dust by 85%, keeping sites compliant.
The disadvantages of air drilling—instability, erosion, fires, and hidden costs—demand rigorous risk assessment. Use it selectively: in hard, dry, hydrocarbon-free formations above 6,000 ft, it outperforms mud. In deep, porous, or reactive-rock environments, its drawbacks eclipse benefits. Always conduct a full feasibility study comparing lifecycle costs—not just daily rates—against alternatives like mist or foam drilling.